Achieve a Zero Incident Goal: Safety First at Work
In today’s fast-changing business world, keeping employees safe is a major focus for smart companies. The idea of a “Zero Incident Goal” is becoming more popular. It shows how important a safe workplace is for a company’s success, employee happiness, and long-term growth.
This approach believes that every workplace accident, no matter how small, can be stopped. By creating a safety-first culture and tackling risks early, companies can keep their workers safe. This also brings many benefits, like better performance and happier employees.
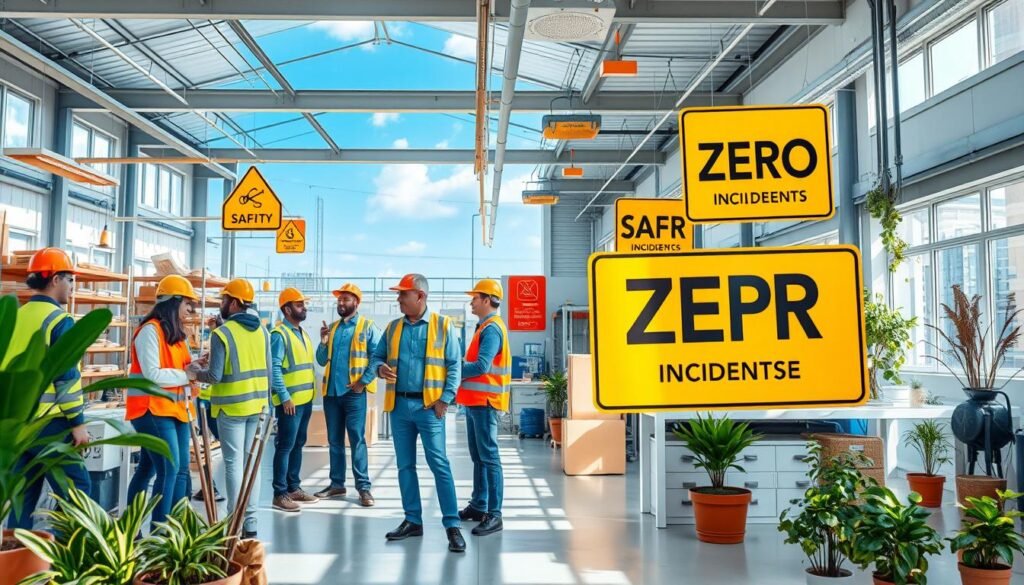
In this article, we’ll explore the Zero Incident Goal. We’ll examine what makes it work, why it’s good for business, and how companies can reach it. We’ll cover the key strategies and systems needed for this goal.
Key Takeaways
- The Zero Incident Goal is a complete safety plan that aims to stop all preventable accidents.
- Putting safety first and building a safety-focused culture can boost morale, cut costs, and improve work flow.
- Good safety management, thorough risk checks, and ongoing training are key to the Zero Incident Goal.
- Reporting incidents, investigating them, and fixing problems are vital for better safety.
- Tracking safety numbers is important to see progress and keep working towards the Zero Incident Goal.
Understanding the Zero Incident Goal Concept
The zero incident philosophy is a new way to think about workplace safety. It aims to stop all accidents and incidents. This idea says that zero incidents is the only goal, not just a dream.
To reach this goal, we need a detailed plan. We must find and fix risks, create a safety-first culture, and keep improving our safety systems.
Defining Zero Incident Philosophy
The zero incident philosophy means working towards a workplace with no incidents. It’s not just about cutting down on incidents. It’s about getting rid of all incidents, big or small.
This idea believes that every accident, near-miss, and danger can be stopped. It’s all about careful planning, good controls, and a focus on safety.
Why Zero is the Only Acceptable Target
Before, many places aimed to lower the number of incidents. They thought some accidents were unavoidable. But the zero incident philosophy says no, any accident is a failure.
By aiming for zero incidents, companies can always get better. Every accident is a chance to find and fix problems.
Breaking Down Safety Excellence Components
- Strong leadership commitment to safety
- Robust safety management systems
- Proactive hazard identification and risk assessment
- Comprehensive employee training and competency development
- Effective incident reporting and investigation protocols
- Meaningful performance measurement and safety metrics
By focusing on these areas, companies can build a strong safety culture. This is the first step towards achieving the zero incident goal.
The path to zero incidents is tough, but the benefits are huge. By following the zero incident philosophy, companies can keep their employees safe. They also get better productivity, lower costs, and a better reputation.
The Business Case for Incident-Free Workplace
Achieving a zero incident goal in the workplace is more than just keeping workers safe. It’s a smart business move that can bring many benefits. By preventing workplace incidents, companies can gain advantages that boost their profits and success.
One big plus of a safe workplace is saving money. Accidents and damage can cost a lot, including medical bills, legal fees, and insurance. There are also indirect costs like lost work time, a bad reputation, and unhappy workers. By avoiding these, companies can save money and use it for better things.
Also, a safe workplace can make a company look good. People like to support businesses that care about safety. This can lead to more loyal customers, better relationships with investors, and a workplace that attracts the best employees.
In the end, aiming for a zero incident goal is a smart choice for businesses. It can improve productivity, save money, and make the company better overall. By focusing on safety and fixing risks early, companies can succeed for a long time.
“Workplace safety is not just a moral imperative, but a sound business strategy. Companies that prioritize incident prevention often see significant returns on their investment.”
In summary, the zero incident goal is a great chance for companies to do better financially, improve their image, and make a better work place. By taking a complete approach to safety, businesses can get ahead and stay successful.
Creating a Proactive Safety Culture
Making a workplace safe is more than just rules and procedures. It’s about creating a culture where everyone works together to prevent accidents. This is key to keeping the workplace safe.
Leadership’s Role in Safety Culture
Leaders set the stage for a safe workplace. They must show they care about safety and lead by example. This means giving resources, empowering workers, and always talking about preventing accidents.
Employee Engagement Strategies
- Encourage employees to join in on safety efforts and make decisions.
- Make sure everyone feels safe to report near misses and dangers without fear of blame.
- Give praise and rewards for safe actions to encourage a culture of excellence.
Communication and Transparency
Good communication is vital for a safe workplace. Open talks between leaders and workers build trust and share knowledge. Regular updates, training, and ways to give feedback keep everyone informed and safe.
“A strong safety culture is not just about numbers and statistics, but about empowering every individual to be a steward of safety in the workplace.”
Creating a proactive safety culture lets workers reach their full potential in keeping operations safe. This approach is the base for lasting success and a safer place for everyone.
Essential Safety Management Systems
To reach a zero incident goal, workplaces need strong safety management systems. These systems include policies, procedures, and protocols. They help spot, assess, and reduce risks to prevent accidents.
At the heart of a good safety system are several key parts:
- Safety Policies and Procedures: Clear, company-wide rules that set safety standards and who’s responsible.
- Risk Assessment and Hazard Identification: Steps to find, check, and tackle possible dangers that could cause accidents.
- Incident Reporting and Investigation: Detailed plans for reporting, studying, and learning from close calls and accidents to improve.
- Training and Competency Development: Wide-ranging training to make sure workers know how to stay safe.
- Performance Measurement and Safety Metrics: Keeping track of safety data to see how well things are going and where to get better.
With these key safety systems in place, companies can stop accidents before they happen. This helps them aim for their zero incident goals.
Safety Management System Component | Description |
---|---|
Safety Policies and Procedures | Clear, company-wide rules that set safety standards and who’s responsible. |
Risk Assessment and Hazard Identification | Steps to find, check, and tackle possible dangers that could cause accidents. |
Incident Reporting and Investigation | Detailed plans for reporting, studying, and learning from close calls and accidents to improve. |
Training and Competency Development | Wide-ranging training to make sure workers know how to stay safe. |
Performance Measurement and Safety Metrics | Keeping track of safety data to see how well things are going and where to get better. |

Also Read: Construction Safety and Health Management Program
By using these important safety systems, companies can stop accidents before they start. This helps them aim for their zero incident goals.
Risk Assessment and Hazard Identification
To reach the zero incident goal, we must be proactive in assessing risks and identifying hazards. By carefully looking at potential risks and tackling hazards, we can prevent accidents. This ensures our employees stay safe at work.
Read: Hazard Identification Plan (HIP) Template
Systematic Risk Evaluation Methods
Starting with a solid risk assessment is key. We use methods like job hazard analysis, failure mode and effects analysis (FMEA), and quantitative risk assessment. These methods help us spot, analyze, and rank risks. This way, we can create plans to reduce and manage risks effectively.
Prevention Through Design
“Prevention through design” is a vital part of our goal. By designing workplaces, equipment, and processes with safety in mind, we can cut down risks. This approach helps prevent accidents before they happen.
Regular Safety Audits
Keeping workplaces safe is an ongoing task. Safety audits by experts help us find new risks, check if safety measures work, and make needed changes. These audits are crucial for improving safety and reaching the zero incident goal.
By using systematic risk methods, designing for safety, and doing regular audits, we can work towards a zero incident goal. This approach helps build a culture of safety excellence in our workplaces.
Risk Evaluation Method | Description | Key Benefits |
---|---|---|
Job Hazard Analysis (JHA) | A systematic process to identify, analyze, and control the hazards associated with specific job tasks. | Helps prioritize risks, develop effective control measures, and engage workers in safety improvements. |
Failure Mode and Effects Analysis (FMEA) | A proactive approach to identifying potential failure modes, their causes, and their effects on system performance. | Enables organizations to anticipate and prevent potential failures, enhancing overall system reliability and safety. |
Quantitative Risk Assessment | A data-driven approach to measuring and evaluating the probability and severity of potential risks. | Provides a comprehensive understanding of risk levels, supports informed decision-making, and prioritizes risk mitigation efforts. |
By following these steps to prevent incidents and always looking to improve, we can make big progress towards the zero incident goal.
Training and Competency Development
Achieving a workplace without incidents is a big goal. It needs a detailed plan for safety management. At the core of this plan is the need for good training and skill development. By teaching your team, you help them play a key role in keeping the workplace safe.
Good safety training is more than just a formality. It teaches your team about safety rules and builds a culture of care. It also gives them the tools to avoid accidents. The training should fit your team’s needs and how they learn best.
Continuous Skill Development
Safety is a journey, not a one-time thing. A program for developing skills keeps your team up-to-date with the latest safety practices. Regular checks, refresher courses, and training in different areas help keep everyone safe.
- Comprehensive training on safety protocols and procedures
- Hands-on demonstrations and interactive learning experiences
- Continuous skill development through assessments and refresher courses
- Cross-training to promote a well-rounded understanding of safety practices
Investing in your team’s training and skill development does more than just keep them safe. It builds a safety culture and makes your team part of your incident-free goals. This approach is key to reaching zero incidents and keeping your team safe.
“Continuous learning and skill development are the cornerstones of a truly incident-free workplace.”
Incident Reporting and Investigation Protocols
Creating strong incident reporting and investigation plans is key to a zero-incident workplace. By tackling near-misses and finding the causes of incidents, companies can learn a lot. They can then take steps to stop these problems from happening again.
Near-Miss Reporting Systems
A good near-miss reporting system helps employees report small issues or dangers early. This way, companies can spot trends and fix problems before they get worse. It helps keep the goal of a zero-incident workplace safe.
Root Cause Analysis Techniques
When an incident happens, it’s important to do a deep investigation. Root cause analysis helps find the real reasons behind the problem. This way, companies can fix the root cause, not just the symptoms.
Corrective Action Implementation
The last step is to put in place corrective actions. These actions should be based on the real causes found. They need to be watched closely to make sure they work. Keeping up with improvements is essential for a zero-incident workplace.
Steps to Prevent Incidents | Key Benefits |
---|---|
1. Implement a robust near-miss reporting system | Identify and address potential hazards before they result in incidents |
2. Conduct thorough root cause analysis | Uncover the underlying issues to develop targeted solutions |
3. Develop and implement corrective actions | Prevent the recurrence of similar incidents and maintain a zero-incident workplace |
By focusing on reporting, investigating, and fixing problems, companies can work towards a zero-incident goal. This promotes a safe culture and ongoing improvement.
Performance Measurement and Safety Metrics
To reach the zero incident goal, a strong system for safety performance is key. By tracking important metrics, companies can spot areas to improve. This helps them make smart choices to keep their workplaces safe. ( Download: E-Books: Leading Indicators for Workplace Health and Safety )
Key performance indicators (KPIs) are at the core of this strategy. These are measurable signs that show how well safety plans work. KPIs might include things like how many incidents happen, how many near misses are reported, and how well employees follow safety rules.
- Incident Rate: Keeping track of work-related incidents is vital. It shows how safe a workplace is and if it’s getting safer.
- Near-Miss Reporting: When employees report near misses, it helps spot dangers before they cause harm. This is a big part of keeping a workplace safe.
- Training Completion: Knowing how many employees have had safety training is important. It ensures everyone knows how to stay safe.
- Safety Audit Compliance: Regular safety checks help find and fix problems. They make sure everyone follows safety rules.
By always checking and looking at these safety numbers, companies can really understand their safety level. They can find ways to get better and make choices based on facts. This helps them work towards a workplace where no incidents happen.
Safety Metric | Description | Importance |
---|---|---|
Incident Rate | The number of work-related incidents, including injuries, illnesses, and fatalities, per a specified time period (e.g., per 100,000 hours worked). | Provides a clear indicator of overall safety performance and progress towards the zero incident goal. |
Near-Miss Reporting | The number of near-miss events reported by employees, which did not result in an actual incident but had the potential to do so. | Helps identify potential hazards and allows for proactive risk mitigation, contributing to the zero incident goal. |
Training Completion | The percentage of employees who have completed mandatory safety training programs. | Ensures a well-informed and safety-conscious workforce, which is essential for achieving the zero incident goal. |
Safety Audit Compliance | The degree of compliance with established safety standards and procedures, as measured through regular safety audits. | Identifies areas for improvement and drives continuous safety enhancements, supporting the zero incident goal. |
By always watching and studying these safety numbers, companies can make smart choices. This helps them create a workplace where no incidents happen. They can reach their zero incident goal this way.
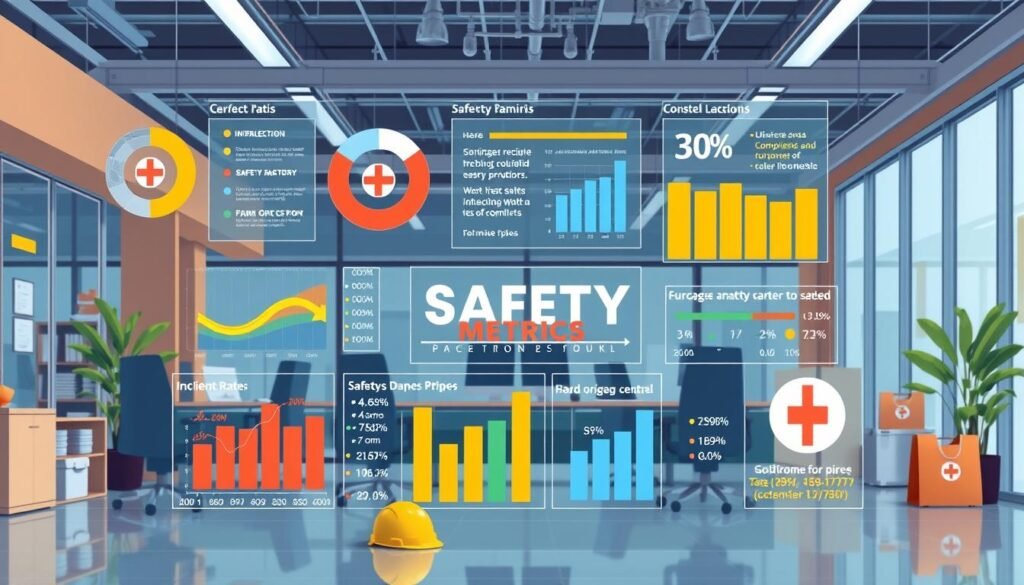
Conclusion
In this detailed article, we’ve looked into the zero incident goal and why it’s so important. It helps make work places safe and productive. By learning about the zero incident philosophy and safety excellence, companies can prevent accidents and build a safe culture.
The benefits of a safe work place are obvious. It keeps employees safe, boosts productivity, cuts costs, and improves the company’s image. To reach this goal, companies need to focus on safety, have strong safety plans, and follow the best ways to handle risks and report incidents.
In wrapping up, it’s clear: aiming for zero incidents is essential for any company that cares about its workers. By following this philosophy and taking action, employers can make sure every worker goes home safely. This creates a positive impact on the whole company and the community.
FAQ
What is a Zero Incident goal?
A Zero Incident goal is a safety aim to have no workplace accidents. It focuses on making the workplace safe by tackling hazards early. This goal is about creating a safe work environment.
Why is the Zero Incident goal important?
It’s key for a safer workplace and less risk of injuries. It also boosts performance and employee happiness. Companies with zero incidents are seen as better places to work.
What are the key components of a successful Zero Incident program?
Success needs strong leadership and a safety-first culture. It also requires good safety systems, risk checks, and training. Plus, reporting and investigating incidents well is crucial.
How can leadership support the Zero Incident goal?
Leaders should show they care about safety and join in safety efforts. They should also give safety resources and lead by example. This encourages employees to focus on safety too.
What are the benefits of implementing a Zero Incident goal?
It reduces injuries and boosts morale and productivity. It also makes the company look better and saves money. Safety is key to success and excellence.
How can organizations measure progress towards the Zero Incident goal?
Track things like injury rates and near-miss reports. Safety checks and investigations help too. This shows how safe the workplace is and where to get better.
What are the steps to prevent workplace incidents?
Start with risk assessments and safety plans. Then, train well and build a safety culture. Good reporting and constant improvement are also vital for zero incidents.
Read:Navigating Your HSE Vacancy: Top Interview Questions and Expert Answers